Advanced metals, materials, and components are extensively utilized by automotive and machine tool manufacturers.
These materials enhance the strength and durability of vehicles and machinery while improving production efficiency and sustainability. Space-age metals and materials like aerospace-grade 6063 aluminum, 304 stainless steel, cold-rolled steel, and cutting-edge composites including carbon and glass-filled nylons are vital elements in globally competitive automotive sectors that contribute to the strength and efficiency of modern machinery and vehicles. Here are some ways that manufacturers use these materials and the benefits they offer.
Aluminum: Lightweight, Versatile, and Adaptable
Manufacturers prize aluminum for its lightweight yet robust properties, making it ideal for automotive and machine tool manufacturing. A highly advanced and versatile material, aluminum is ideal for automotive and machine tool manufacturing, among many others. Some automakers use aluminum in different manufacturing processes widely due to its lightweight, high strength-to-weight ratio, and excellent corrosion resistance. Lean methodologies in manufacturing have also been used to maximize efficiency. The versatility of aluminum extrusions allows manufacturers to create complex shapes and profiles that are integral to innovative designs.
Examples of Aluminum in Automotive Manufacturing:
- Chassis and Frame Components: The lightweight nature of extruded aluminum helps in reducing the overall weight of vehicles and may improve fuel efficiency and handling.
- Body Panels: Using extruded aluminum reduces vehicle weight, enhancing fuel efficiency and performance.
- Engine Components: Aluminum’s excellent thermal conductivity suits it for some engine parts that require heat dissipation.
Key Uses in Machine Tool Manufacturing:
- Machine Bases and Frames: Extruded aluminum profiles provide sturdy yet lightweight structures, improving machinery mobility and flexibility.
- Tooling Components: The precision extrusion of aluminum allows for producing high-quality tooling components that maintain accuracy and consistency.
Stainless Steel Tubes: Metal with Strength and Corrosion Resistance
Stainless steel tubes provide exceptional strength, corrosion resistance, and durability, making them essential in both automotive and machine tool industries. They perform well in high-temperature and corrosive environments.
Some Uses of Stainless Steel in Auto Manufacturing:
- Exhaust Systems: Stainless steel’s resistance to high temperatures and corrosion makes it ideal for exhaust components.
- Structural Components: The strength and durability of stainless steel tubes ensure the structural integrity of various vehicle parts.
Uses in Machine Tool Manufacturing:
- Hydraulic Systems: Stainless steel tubes deliver strength and resistance to wear and tear in hydraulic systems.
- Support Structures: The robustness of stainless steel ensures the stability and longevity of machine tool frames and supports.
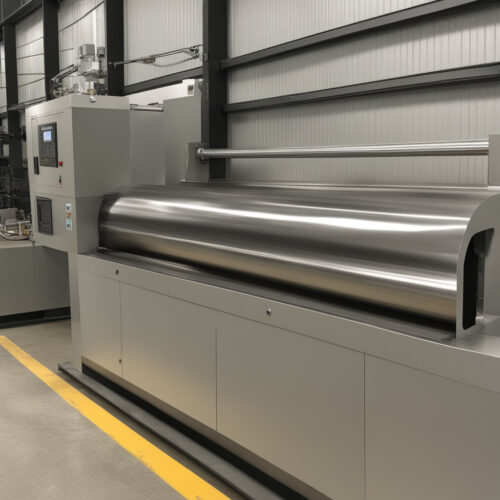
6061 aluminum and 6063 extruded aluminum tube form the basis for machine tool and die industry machine guards
Steel Tubes: A Metal for Durability and Cost-Effectiveness
Steel tubes, including 1 inch square tubing, are prized for their durability and cost-effectiveness. It is available in various sizes and shapes, such as 1×1 square tubing, 2×2 square tubing, and 3×3 square tubing, making them adaptable to numerous applications.
Key Uses of Steel in Car Manufacturing:
- Chassis and Suspension Components: Steel tubes provide the necessary strength and rigidity for critical structural components.
- Roll Cages: In motorsports and high-performance vehicles, steel tubes construct roll cages that protect occupants in case of a rollover.
Key Uses in Machine Tool Manufacturing:
- Structural Frames: Steel tubes form the backbone of many machine tool frames, providing the necessary support for precision operations.
- Transmission Systems: Steel’s strength makes it ideal for use in the transmission systems of heavy machinery.
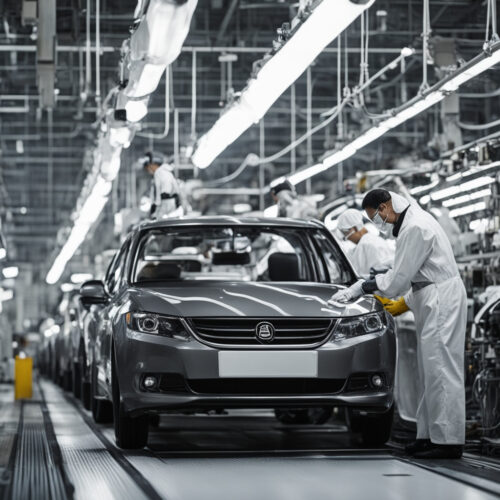
Space-age composites and premium alloys like aerospace-grade aluminum, high-grade steel, and durable stainless steel form the basis for the future of auto manufacturing
Composite Fasteners: Advanced Solutions for Global Markets
Manufacturers increasingly use composites due to their lightweight, non-corrosive, and high-strength properties. These fasteners reduce the overall weight of assemblies while maintaining structural integrity. They offer an advanced solution for joining different materials, providing reliability without adding significant weight.
How are Composites Used by Automakers?
- Assembly of Lightweight Components: Composite fasteners are essential in applications where weight reduction is critical, such as in automotive interiors and certain machine parts.
- Corrosion-Prone Environments: Their resistance to corrosion makes composite fasteners suitable for use in environments where traditional metal fasteners would degrade quickly.
- Body Assemblies: Composite fasteners reduce weight without compromising the strength of body panels and assemblies.
- Interior Components: They use these fasteners in interior components where reducing weight is crucial for overall vehicle efficiency.
Advanced Composite Uses in Machine Tool Manufacturing:
- Modular Assemblies: Composite fasteners allow for easy assembly and disassembly of modular machine components, enhancing flexibility in manufacturing.
- Vibration Damping: Their material properties help reduce vibrations, improving the precision of machine tools.
Integrations in the Manufacturing Processes
Automotive Manufacturing:
- Frame Construction: The integration of 1 inch square tubing, metal tubing, and extruded aluminum in frame construction provides a balanced mix of strength, durability, and weight reduction.
- Exhaust Systems: Stainless steel tubes ensure that exhaust systems are both durable and efficient, contributing to the overall performance of the vehicle.
Machine Tool Manufacturing:
- Tool Frames and Supports: Steel tubes, such as 1×1 steel tubes and 2×2 square tubes, are used to build robust frames and supports for various machine tools.
- Protective Enclosures: Extruded aluminum is often used to create lightweight yet sturdy protective enclosures for machinery, ensuring operator safety and equipment longevity.
Cost and Availability of Metals in Manufacturing
Understanding the cost and availability of these materials is crucial for manufacturers. For instance, the price of 1 square tubing can vary based on the material (steel or aluminum), dimensions, and supplier. For larger applications, such as the construction of machine frames, the cost of 2×2 square tubing 20 ft price must be considered to ensure budget compliance. By purchasing these advanced metals from a trusted material supplier such as EZ Tube, or from a premier global distributor, automotive manufacturers can maximize the efficiency of their supply chain and work towards a more sustainable future of manufacturing.
EZ Tube for Advanced Manufacturing Solutions
By using extruded aluminum, stainless steel tubes, steel tubes, and composite fasteners in automotive and machine tool manufacturing, the benefits and importance of material selection in modern engineering becomes even more evident. Each material offers unique advantages that, when combined, result in products that are strong, durable, and efficient. By leveraging the properties of these materials, manufacturers can continue to innovate and improve the performance and reliability of their products.
Whether it’s the lightweight efficiency of extruded aluminum, the robust durability of steel tubes, or the advanced solutions provided by composite fasteners, these materials are becoming indispensable in driving forward the capabilities of the automotive and machine tool manufacturing industries.